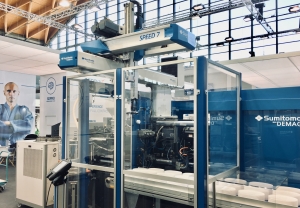
Under its “Experience Full Control” banner, Sepro Group is presenting a series of demonstrations and exhibits that harness the power of collaboration to achieve new levels of productivity, quality and flexibility in plastics injection molding. Sepro is exhibiting in Hall 12, Stand A49 at K 2019, the world’s largest plastics show, which is being held October 16 – 23 at Messe Dusseldorf in Germany.
A total of eight robots are operating on the stand, including 3-, 5- and 6-axis models, as well as collaborative units (cobots), provided through a recently announced partnership with Universal Robots. Several of the robots will be part of automation cells centered on two operating injection-molding machines. Sepro products also can be seen operating on the stands of eleven IMM partners exhibiting at the show.
“A large part of Sepro’s recent growth is thanks to the breadth of technology we offer as a result of collaboration with injection-molding machine makers and other automation companies,” notes Eric Radat, President of Sepro Group. “It is what makes it possible for our customers to ’Experience Full Control,’ and it is on full display in Dusseldorf this October.”
Molding Cells
One of the two automation cells on the stand features a Sumitomo Demag molding machine producing a technical component that will be removed from the mold by an SDR Speed 7 robot. Made by Sepro especially for sale with Sumitomo Demag machines, this robot, is a special high-speed version of Sepro’s S5-25 3-axis Cartesian robot capable of getting in and out of the mold space in under 1 sec.
The other molding cell includes a Sepro – Universal Robots cobot together with a Sepro Success 11 Cartesian robot operating on a molding machine from Haitian International that is producing drinking cups using a mold supplied by French mold maker SIMON. As the cups are molded, visitors watching the demonstration can enter a brief message (a name, for instance) to be printed onto a label using a system provided BluhmWeber Group. The cobot then applies the label and hands the personalized cup to the visitor. In keeping with the K fair’s “Circular Economy” theme, the label and the cup are recyclable.
A second cobot will be running in a stand-alone demonstration of robot/human interaction. Visitors to the booth are invited to choose between a round box of candy and a square one. With the help of a flexible-feeding system — provided by the Swiss company Asyril SA – and input from a machine-vision camera, the cobot picks the appropriate shape and places it on a table where the visitor can retrieve it.
Redesigned Success Robots Deliver Affordable 5-Axis Option
A prototype of a new 5-axis-servo version of its updated Success Line of robots is being shown for the first time at K 2019. The Success 22 X combines a redesigned Success 3-axis Cartesian platform with a 2-axis servo wrist co-developed with Yaskawa Motoman. Slated for introduction in Q3 2020, the Success Line X offers a new level of performance in general-purpose robotic automation for IMMs from 20 to 700 tons. For more advanced applications, the Sepro 5-axis offering already includes the 5X Line of small and mid-size robots and the 7X Line of large robots.
“My Gripper” Makes Sourcing EOAT Component Simple
Through an imaginative collaboration with Gimatic and AGS, Sepro now offers one-stop access to over 700 components used in building robotic end-of-arm tooling (EOAT) for plastic injection-molding applications. The My Gripper system enables easy selection of compatible EOAT components, including structural parts, vacuum cups, sprue-cutting elements and a whole range of tooling accessories. A 66-page My Gripper catalog gives molders easy access to more components from a single source than ever, all backed by advice and technical support from Sepro locations worldwide.
Visual Dashboard and Visual Plant, Featured in ‘Sepro Lab’
Visual Dashboard is a ‘smart data’ solution that harnesses the power of Sepro’s Visual robot control to collect real-time production data from an IMM served by a Sepro robot. Data include cycle times, mold-open times, and production and quality rates essential to calculating Overall Equipment Effectiveness (OEE). The data collected on several cells can be gathered on an existing MES or integrated on a dedicated platform. During the K Show, the system will present data collected from the operating molding machines in Sepro’s booth on a demonstrator called Visual Plant. This system can aggregate data even from older IMMs and from machines from different manufacturers.
The Visual Dashboard and the Visual Plant demonstrator are available to visitors to try out in a special ‘Sepro Lab’ section of the stand. The space is dedicated to new and existing projects aimed at providing technologies that make it easier for molders to use Sepro robots efficiently and profitably. Also available for guests to use are:
- Open integration: the Sepro’s robots can be implemented on any IMM and, with the “Easy Package” approach, seamless integration into the IMM controls is possible.
- OptiCycle, the Sepro wizard that helps programmers develop a standardized and optimized robot cycle
- Live Support, a smart-device application that streamlines robot troubleshooting and maintenance to maximize uptime.
- Experience the user-friendliness of Visual control
Other Sepro Robots at K 2019
The Sepro commitment to integration and collaboration now makes it possible for injection molders to get packaged machine/robot solutions through manufacturers from Germany, Japan, China, USA, France and elsewhere. At K 2019, more than a dozen different IMM suppliers are operating Sepro robots on their own machines. These include:
EXHIBITOR |
COUNTRY |
STAND |
Sumitomo Demag |
Japan/Germany |
15-D22 |
Haitian |
China |
15-A57 |
Billion |
France |
15-B24 |
Romi |
Brazil |
15-D40 |
Chen Hsong |
China |
13-B43 |
Tederik |
China |
15-A41 |
Woojin Plaimm |
Korea |
15-D58 |
JSW |
Japan |
13-B45 |
Lien Fa |
Taiwan |
13-D40 |
Kurtz |
Germany |
13-B27 |
Bole |
China |
15-B59 |
Download and read the full press release below.
Download Text Documents
Download Photos
Back to Press Releases